In 2019, an Indiana metal parts manufacturer welcomed a group scouring their business in an audit – to help the company save money.
Metal Forming Industries received more than $6,000 in Power Moves® rebates from Parke County REMC, its electric cooperative, for upgrading to LED lighting in its Russellville, Ind., facility. The company also received a free commercial energy audit from Parke County REMC. The audit, in partnership with Purdue University, included a review of the facility and analysis of the structure’s energy use to create an action list for the company to reduce long-term energy use and save money.
“The audit just reinforced what we needed to do,” said Diane Fordice, plant manager for Metal Forming Industries. “We put occupancy sensors in the production support areas, for instance. It was a lot of small things that had a big impact on our staff.”
The high bay LEDs installed in the production areas were much brighter than the lights that were replaced, Fordice said. Because of that, additional task lights that had been at each machine were removed.
“Literally before that, we had lights on every piece of equipment,” Fordice said. “There were just tons of light fixtures, so we were using more electricity. And the morale was much better once we started putting the LEDs in.”
Metal Forming Industries employees first started speaking with Parke County REMC employees about power concerns in 2014. They discussed the Power Moves program and the company received its first rebate in 2017. They have regularly met with the cooperative’s energy advisor who provided insight on projects that would qualify for the Power Moves rebates since then.
“It’s been great. It’s seamless for me,” Fordice said of working with Parke County REMC on the Power Moves rebates. “My job in that was very small. It’s great because I don’t have the time.”
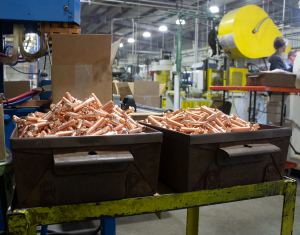
The co-op also provided insight into the electricity usage of the company’s manufacturing equipment. The cooperative’s staff analyzed Metal Forming Industries’s energy consumption, and after reviewing the business’s facility, advised them to invest in a capacitor, which helps regulate the flow of electricity to connected equipment. Some of the manufacturing
equipment was causing Metal Forming Industries to have a low power factor, or a measurement of how effectively energy is used. The capacitor, which regulates the flow of electricity to machinery, helped Metal Forming Industries save nearly $500 in monthly energy costs.
“Metal Forming Industries is an internationally successful business that we are proud to serve,” said Chadd Jenkins, president and CEO of Parke County REMC. “They have been receptive to more efficiently and effectively using energy. We are committed to helping all of our members, including families and businesses, to be successful.”
Metal Forming Industries employees continue to meet with Parke County REMC’s energy advisor several times per year to discuss ways that the business can improve its energy use. Metal Forming Industries uses savings and rebates from previous Power Moves projects on subsequent projects to compound on their savings investments.
“Anything comes up, we check with Parke County REMC, because anything we buy could affect what we do in terms of energy, and if there are any rebates available,” Fordice said. “It’s in our minds to call and talk with the REMC to see what would happen.”
PROJECT
• Installation of LED lighting and fixtures in facility
• Commercial energy audit for manufacturing facility
LOCAL PARTNERS
• Parke County REMC
PARTNERSHIP HIGHLIGHTS
• Power Moves rebates for energy efficiency upgrades to facility, saving 66,257 kilowatt-hours annually
• Facilitated technical assistance to support manufacturing equipment to use energy more efficiently
• Performed energy audit of facility providing recommendations on projects to improve energy use
FINANCIAL IMPACT
• $6,062 in Power Moves rebates for energy efficiency upgrades to facility
• $6,000 in annual energy savings from projects, addition of capacitor to equipment
Download the full Metal Forming Industries Case Study.